HIER IST DER STOFF FÜR DIE ZUKUNFT.
Eine grüne Mobilität mit Wasserstoff und Brennstoffzelle. Versorgungssicher und umweltverträglich. Dafür setzen wir uns als starke Industrie-Partnerschaft ein. Das Besondere: Hier arbeiten Technologie-, Mineralöl- und Energiekonzerne, Gasproduzenten und Automobilhersteller branchenübergreifend zusammen. Vereint im Ziel, innovativ und zukunftsorientiert.
Wir finden Lösungen, wir normieren und setzen Standards. Wir sind überzeugte Macher, agieren als Think Tank und Wegbereiter. Wir kommunizieren Technologie und stehen der Politik beratend zur Seite. Wir haben gute Argumente. Wir sind auf dem Weg. Wir sind nicht zu stoppen. Wasserstoff ist nicht zu stoppen.
Unsere Lösung für eine erfolgreiche Energie- und Verkehrswende? Natürlich Wasserstoff!
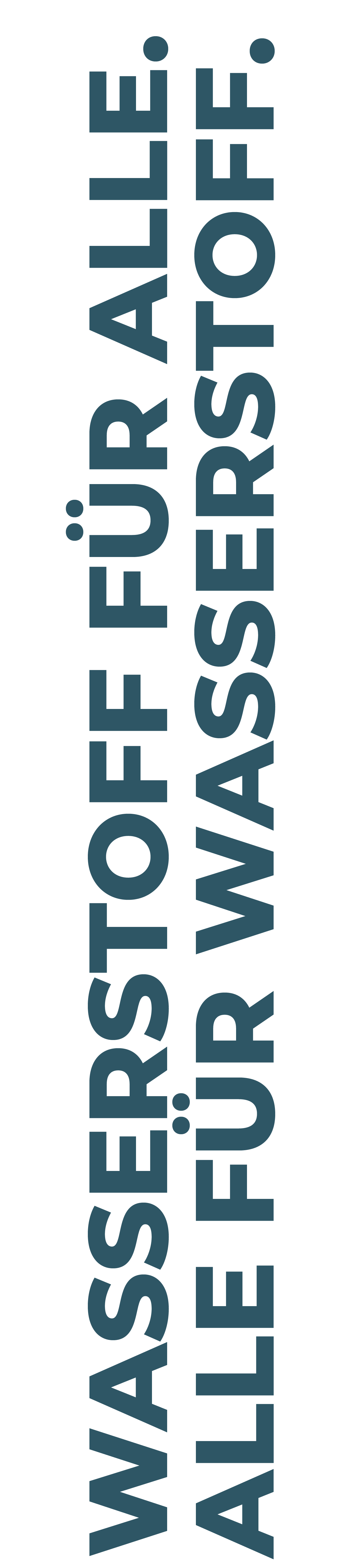

WASSERSTOFF FÜR ALLE. ALLE FÜR WASSERSTOFF.
Unser Herz schlägt für die H2-Mobilität. Unsere Stärke? Unser Team mit jeder Menge Know-how und Erfahrung. Gemeinsam arbeiten wir an unserem Fokusthema: Effiziente Normungs-Lösungen für eine optimale H2-Betankung – natürlich verkehrsträgerübergreifend.
Wir haben genau hingesehen, Fahrzeugdaten, Anlageneffizienz und das Zusammenspiel aller Komponenten geprüft. Dank unserer gesammelten Erfahrungswerte, durch Forschung und Entwicklung haben wir maßgeblich zur Definition des weltweit gültigen Standards für 700 bar-Betankungen SAE TIR J-2601 beigetragen. Pkw und leichte Nutzfahrzeuge bis zu einer Tankgröße von 10 kg können dadurch im Kontext eines allgemein anerkannten Standards betankt werden. Ein großer Schritt. Aber wir wollen mehr.
Wir sind Überzeugungstäter und haben noch viel vor. Denn wir wissen um das große Potential von Wasserstoff und Brennstoffzelle für die Mobilität. Ob Pkw, Busse, Lkw, Züge oder andere Verkehrsträger, wir arbeiten an der Betankungstechnologie – auf Fahrzeug- und Zapfsäulenseite.
Dabei sehen wir als Ziel das Big Picture, from well to wheel. Die gesamte Wirkungskette effizienter und kostengünstiger zu gestalten, das ist unser Anliegen. Angefangen bei der Energieerzeugung, über das Fahrzeug und die Tankstelle bis hin zur Logistik.
KOMMUNIKATION FÜR MEHR SICHTBARKEIT
Wir haben etwas zu sagen. Unsere Erfahrungswerte zeigen: Wasserstoff ist unsere Chance auf eine erfolgreiche Energie- und Verkehrswende. Gut zu wissen, oder?! Und genau deswegen kommunizieren wir. Um zu informieren, zu überzeugen und zu begeistern.
Wasserstoff ist eine Antwort auf den kollektiven Wunsch nach einer verantwortungsvollen Mobilität und einem CO2-neutralen Lifestyle. Wir machen die Transformation der Mobilität sichtbar und informieren über den neuesten Stand der Technologie. Wir sind am Puls der Zeit und entwickeln neue Formate, informieren digital wie analog. Mission started!

GUTE ARGUMENTE FÜR EINE STARKE H2-POLITIK
Die Technologie hat den Status der Marktreife erreicht und die Nationale Wasserstoff-Strategie (NWS) wurde erfolgreich verabschiedet. Jetzt gilt es im Schulterschluss von Politik und Industrie die regulatorischen Rahmenbedingungen für eine zeitnahe und umweltverträgliche Etablierung am Markt zu schaffen. Was uns außerdem wichtig ist? Eine wirtschaftlich abbildbare und versorgungssichere Produktion grünen Wasserstoffs zu ermöglichen. Wasserstoff ist Teil der Lösung. Dieses Potential müssen wir nutzen, gemeinsam!